Dental Lab Outsourcing: The Good, the Bad, and the Ugly
By Robert Winter on May 9, 2022 | comments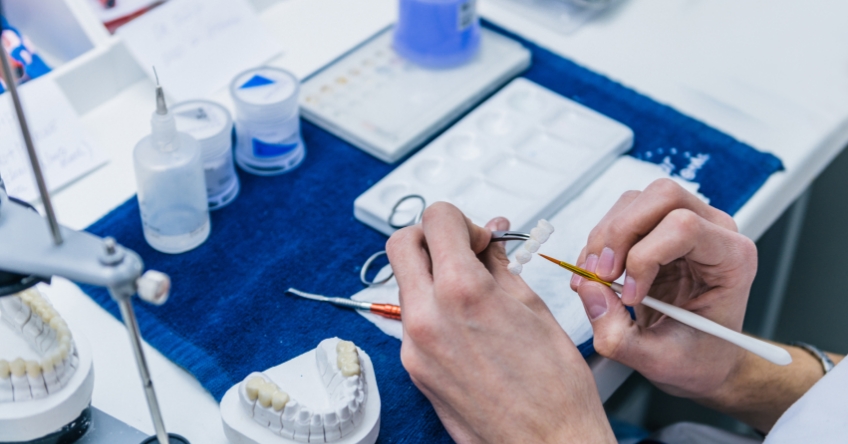
The cost of dental materials and the shortage of dental technicians in the United States has increased significantly in recent years, and some labs simply cannot continue to service clients in the same manner without increasing their prices. Due to this, dental lab outsourcing has become a more standard practice. Many small and large labs fabricate their restorations or appliances in the United States. However, without disclosing information to their clients, a growing number of dental labs are outsourcing the fabrication of their restorations to overseas laboratories.
Your lab partnership is an important part of your budget and affects the services you provide to your patients. By having a better understanding of the good, the bad, and the ugly of why labs outsource, you can provide the highest level of care to your clients at the most competitive price.
Many labs fear increasing prices will drive their client base to a less-expensive competitor. The cost of producing restorations offshore is a fraction of the price of fabricating them in the United States, so outsourcing is one way for a lab to increase profits while maintaining current pricing.
While many people think of outsourcing facilities as being located predominantly in China, U.S. labs may also send their work to countries like Vietnam, India, Thailand, and South Korea. It is important to understand the disclosure regulations in your state regarding their use. Currently, only a few states require dental labs to inform their clients if they use an offshore laboratory to fabricate their work.
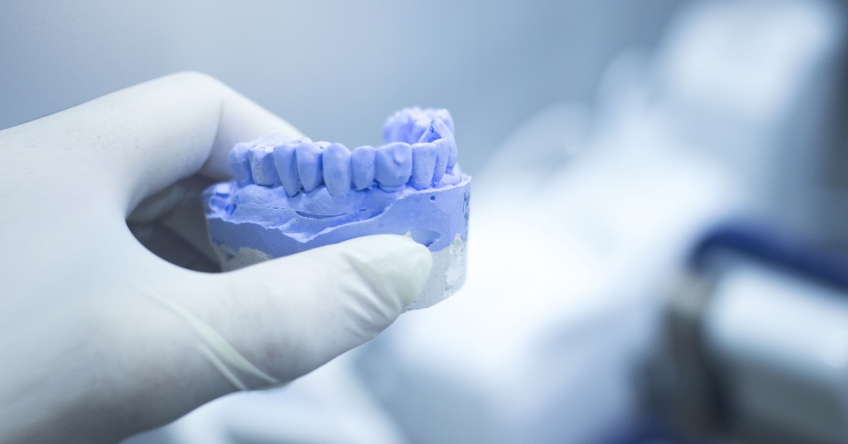
'The Good' Aspects of Dental Lab Outsourcing
Outsourcing to a U.S. or overseas lab can increase profit margins for the laboratory. If the lab is upfront with their clients regarding where their restorations are produced and the materials used during the fabrication process, there is nothing wrong with this practice.
Due to the cost of purchasing equipment and investing in new technology, many labs rely on outsourcing at least some of their work to compete in today's market. Many small labs simply do not have the financial ability to purchase scanners, CAD/CAM machines, or 3D printers. By outsourcing some of their work, they can offer more services than they could if they did all the work in-house, improving the number of products they offer.
'The Bad and The Ugly' Aspects of Outsourcing
Outsourcing also has its drawbacks. According to a study published by the American Dental Association (ADA), 20 percent of dentists at that time did not know their restorations were being outsourced overseas by their local lab. Since then, this number has been predicted to have grown exponentially.
According to the ADA, some of the dental restorations produced offshore have been found to contain products dangerous or harmful to patient health. Issues they have identified include:
- The common use of toxic/dangerous materials, such as lead.
- The risk of contamination within the restoration and dental work itself.
- Low-quality fabrications with poor durability.
- Crowns, implants, and bridges are tainted with compounds not authorized for use in the United States.
Another factor that needs to be considered is whether the offshore lab is following strict infection control guidelines that meet U.S. standards. Due to a lack of regulation in many countries, infection control procedures we take for granted in the United States may not be followed, increasing the potential for complications and restorative failures.
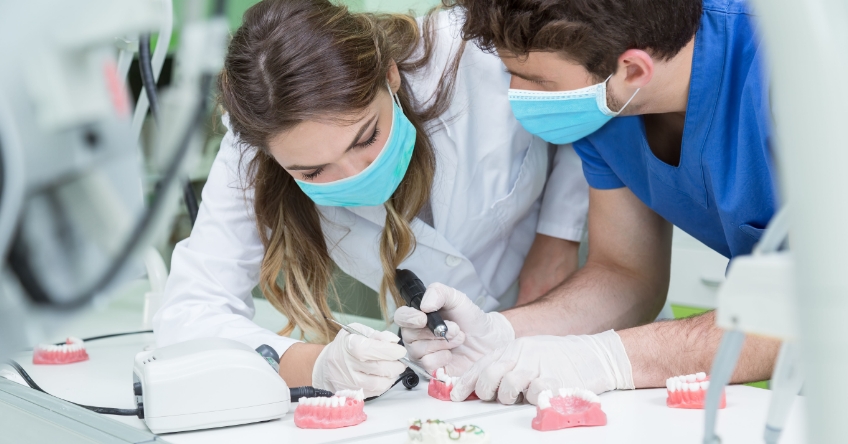
Ensuring the Quality of Your Lab
If the source or quality of the restorations and appliances you deliver to your patients is a priority or concern, here are some questions to ask your lab and steps to take to help ensure you know where your restorations are produced and what materials are used.
- Ask if they outsource any part of their work or if any of the outsourcing is to an offshore lab.
- If they are using an overseas lab, ask what portions of the fabrication process or products are outsourced. Request the FDA registration number of the lab they are using.
- Request documentation of the materials used by the offshore lab and request proof that the materials are FDA approved and compliant with ANSI and ISO standards.
- Request a copy of the overseas lab's quality and infection control policies and standards.
- Ask if they are using name brand or original materials and implant parts.
You should also check with the manufacturer of the parts and materials you request from your lab to see if the lab is a current client. If they are not, it may be a red flag.
If your lab is outsourcing their work, you may want to ask for written indemnification and assumption of liability in the event of claims for any injuries caused by the dental restorations or the materials which were used to produce them.
In the end, you are responsible for what you insert in your patient's mouth, so you must understand “the good, the bad, and the ugly” associated with your lab and whether dental lab outsourcing is impacting your bottom line.
Robert Winter, D.D.S., is a member of Spear Resident Faculty.